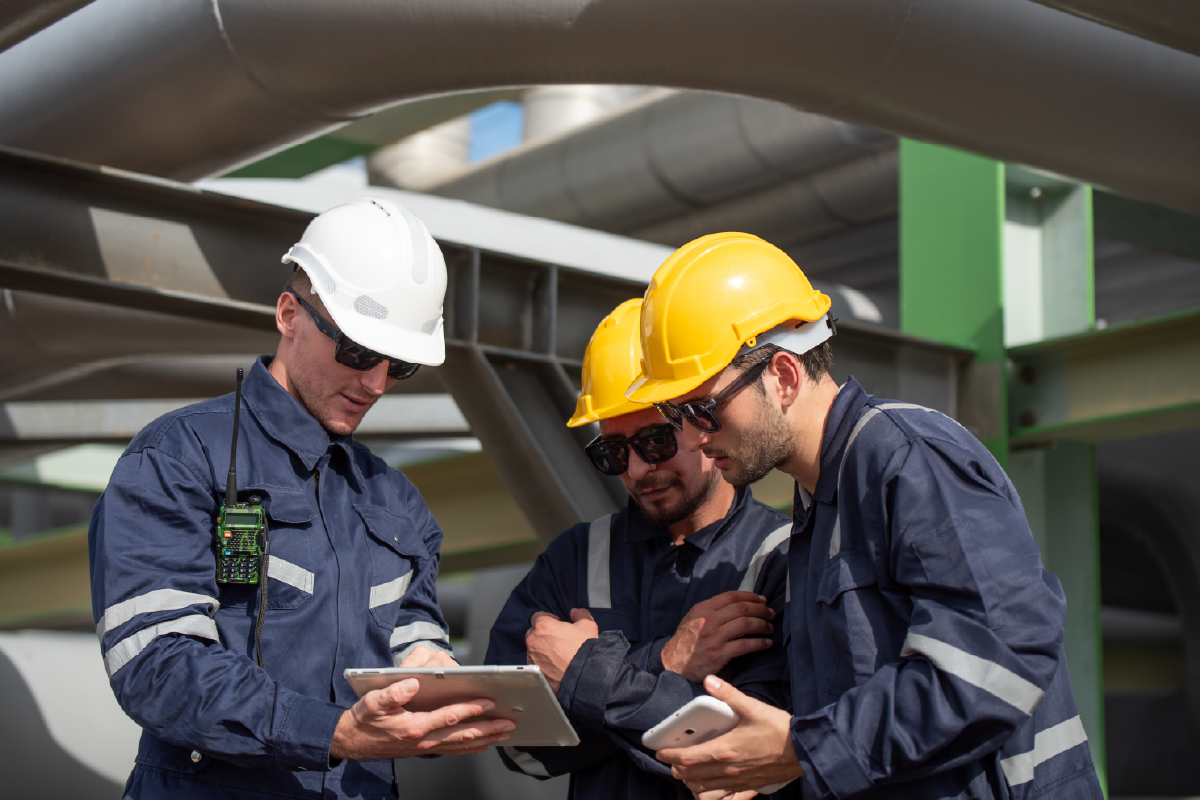
You rely on your heavy machinery to keep your customers happy, your team employed and your revenue flowing. Emergency maintenance is expensive, but the longer you operate industrial equipment without taking proactive measures, the more likely an unplanned emergency—a shutdown—becomes.
To make matters more complicated, winter weather creates new hazards, further threatening the continued operation of your business. Components ranging from bearings to fluids (like oil or lubricants) can experience a greater risk of failure when temperatures drop. Regular predictive maintenance checkups, however, can mitigate some of that risk.
At Cornerstone Mechanical, we can create a comprehensive predictive maintenance program for your facility’s rotating equipment. Our team will help identify any possible points of failure and recommend solutions to avoid an unplanned outage. Our trained technicians use highly accurate tools, such as vibration monitoring and infrared thermography, to make sure that your machinery is in top working order.
Common Component Failures in the Winter
A change of even a few degrees in the average operating temperature of your machinery could cause some serious problems. Even if most or all of your machines reside indoors, the winter weather finds a way of creeping in.
During the colder months, certain machine components may be more likely to suffer from the sub-zero temps. Here’s a brief (and by no means exhaustive) list of components that are in special danger throughout the winter months:
- Filters (fuel/air)
- Fluids (oils and other lubricants become thicker—consider the freezing point of lubricating oil)
- Seals
- Hoses
- Temperature control systems
- And more
Cornerstone’s reliability technicians can perform predictive maintenance services to identify certain components that need repair or replacement due to winter weather.
Predictive Maintenance Services
Cornerstone Mechanical performs regular preventive maintenance and predictive maintenance for industrial equipment to ensure bearings are properly lubricated and pump/gearbox oil has been changed. Cornerstone reliability technicians use comprehensive predictive maintenance best practices and high-tech equipment for vibration monitoring.
Vibration monitoring and analysis allows the Cornerstone team to identify possible problem areas based on the vibration of your machine and its components, preventing problems before they become failures. This also gives you the time you need to source the necessary parts and schedule factory maintenance services when it’s convenient for you—a task that Cornerstone is also happy to help with.
For ideal results and maximum operational output throughout the winter months, Cornerstone’s predictive maintenance services include cutting-edge methods to ensure your equipment’s performance exceeds expectations. For this reason, we also employ infrared thermography and oil analysis as part of our program options.
No two operations are alike, which is why we’ll design a custom predictive maintenance program to fit your machinery’s unique needs. This gives you the certainty you need to charge forward all winter long! Call us to schedule a site visit and take the next step toward boosting your equipment’s performance during the winter months.