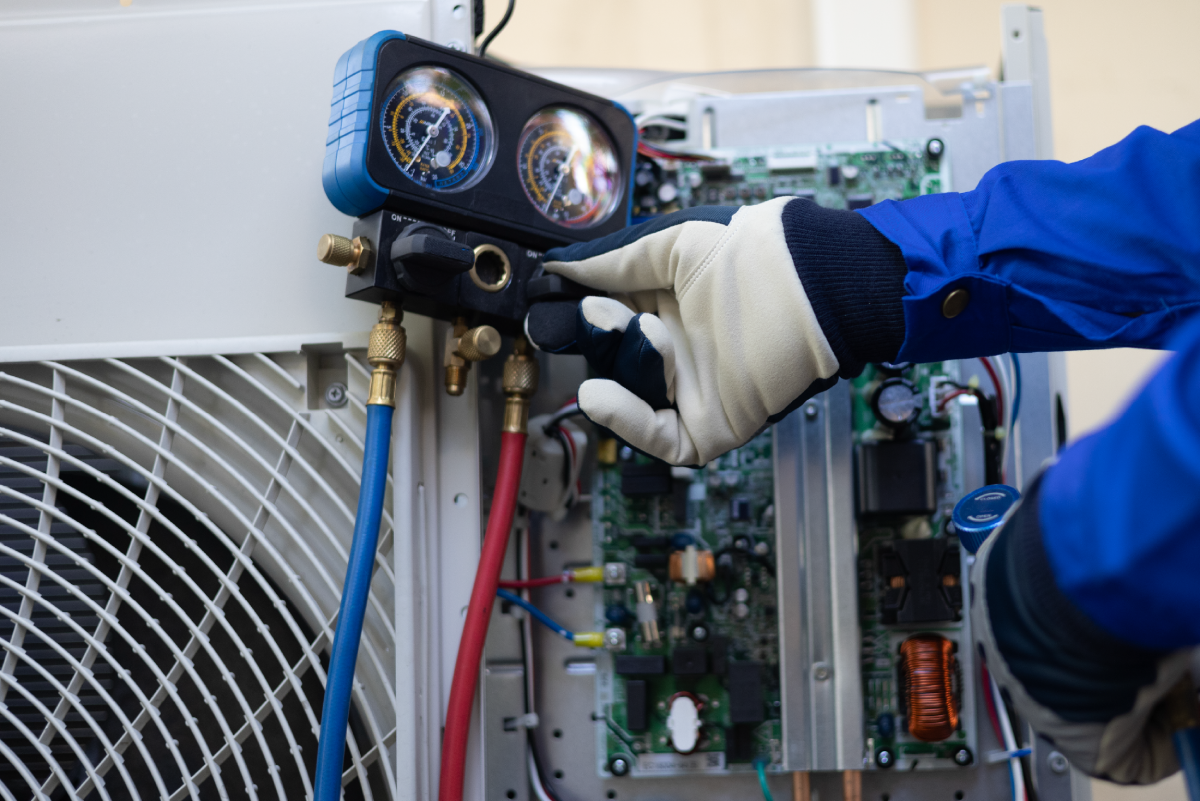
Table of Contents
Component failure is inevitable. Every piece of machinery will undergo some form of wear and tear over the course of its lifetime, no matter what you do. Thankfully, although component failure and its causes aren’t preventable, they are predictable. That’s where Cornerstone Mechanical’s maintenance services for rotating equipment come in.
Predictive maintenance services help determine when a component may fail, giving you more time to prepare for either component repair or total equipment replacement. You can order any necessary parts and plan for when a shutdown has to occur. In other words, your equipment is at your mercy and not the other way around. Here are some of the most common causes of machine failure and how to anticipate them before they result in unexpected downtime.
Top Causes of Machine Failure
Overheating
From electrically overloaded motors to poorly ventilated compressors, many machine components and pieces of rotating equipment can fail due to overheating. The common denominator in most cases of components and equipment becoming overheated is the generation of excessive friction.
Friction will always exist in rotating equipment where surfaces are in contact with each other and there is relative motion. Bearings are meant to prevent direct metal-to-metal contact and reduce friction, heat generation and wear and tear between moving parts. However, when bearings become worn down over time, they fail to protect these components. Monitoring when bearings need to be replaced is imperative to maintaining the health of your rotating equipment and achieving reduced wear and failure of machine components.
Overheating can’t always be chalked up to excessive bearing temperature. High electrical resistance, faulty electrical components and localized heating within a motor are a few of several issues that could be the root cause of your rotating equipment’s failure. Cornerstone’s expert technicians have the ability to identify problem areas like these by performing infrared thermography inspection services before they cause unexpected shutdowns.
Additionally, couplings are meant to connect shafts and protect bearings by reducing stress caused by excessive vibration or misalignment. If couplings gradually become loose, components become misaligned and can cause overheating due to excessive contact. Cornerstone Mechanical’s reliability technicians provide laser alignment services to finely tune 8,000 hp compressors and fractional motor pumps with equal precision, giving you peace of mind that no undue heat sabotages your bottom line.
Misalignment
When couplings become misaligned, they cause the shafts that connect so many components of rotating equipment to become misaligned as well. Whether it’s a compressor and a motor or a fan and its blades within an air handler unit being misaligned, this seemingly small problem can cause far larger issues for your machinery if ignored.
Thankfully, Cornerstone’s reliability technicians provide laser alignment services to meticulously align machine components before excessive vibrations and premature bearing, coupling or shaft failure occur within your rotating equipment.
When you call on our team to perform laser alignments, you not only receive top-of-the-line service, but also easy-to-read alignment reports that document your equipment’s as-found and as-left alignment values, shim changes and horizontal movement of machinery feet to keep a log of your equipment’s alignment for future maintenance services.

Imbalance
Rotating components of machinery may become destabilized, or imbalanced, due to a rotor’s center of gravity and center of rotation being misaligned. Imbalanced fan wheels and rollers, conveyor screws, hammermills and a variety of other components can all create intense vibrations, significantly contributing to the risk of overall machine failure.
However, most pieces of machinery display some level of vibration. The question is: how do you know when your equipment’s vibrations are abnormal? With the expertise of Cornerstone Mechanical’s vibration analysts and our vibration monitoring and analysis services, you can more easily determine speeds at which your equipment is operating at a critical level, spot when your equipment requires dynamic balancing and predict when equipment failure may occur so you can schedule necessary maintenance services and stay ahead of the curve.
If your equipment requires dynamic balancing services to get rid of intense vibrations, our team of reliability technicians will come to you with our state-of-the-art balancing machines to diagnose what’s causing the vibrations and balance your equipment thoroughly and efficiently.
Lack of Regular Maintenance
Between the pressure to meet clients’ expectations, a busy production schedule and meeting quarterly goals, it’s understandable that scheduling regular maintenance may fall by the wayside. However, you can’t understate the importance of regular maintenance for your rotating equipment to improve its long-term health and performance. You visit your doctor regularly to keep your preventive care services up to date, so why should you treat your rotating equipment differently?
A lack of regularly scheduled maintenance can accelerate the impacts of regular wear and tear on your rotating equipment. By scheduling maintenance ahead of time, you can monitor machine component failure more easily and decrease the risk of work stoppages, emergency repair costs and injuries. Whether you’re struggling with worn bearings, damaged impellers, or a leaky pump, compressor or gearbox, Cornerstone Mechanical’s experienced team of technicians is eager to help you get back to business as quickly as possible.
The eventual failure of machine components may be unavoidable, but unanticipated downtime doesn’t have to be. By partnering with Cornerstone Mechanical Services and implementing a predictive maintenance program for your facility, you gain a proactive edge over misalignments, imbalances, overheating and regular wear and tear.
Call us at 214-225-7038 to learn how the Cornerstone Mechanical team can help you combat surprise shutdowns and improve the longevity of your rotating equipment.